By Natalie Landrito, Marketing & Public Relations Manager, Motion Business Area
APRIL 4, 2024
The brewing industry faces several challenges, including changing consumer preferences, more competition, volatile energy supply and prices, and rising costs of raw materials.
According to the Australian Craft Beer Brewery list in 2018, a new craft beer brewery was established every six days in Australia. The growth in the number of brewery locations can be attributed not only to the growing consumer demand for high-quality and unique beer varieties but also to the breweries’ desire to be more accessible to customers and improve their manufacturing operations to reduce distribution costs. By 2023, the beer manufacturing industry in Australia had grown significantly, reaching a market size of $1.5 billion*.
In 2024 however, the industry is in a tumultuous period. Many breweries are shutting down due to several factors, such as the high cost of operations, a decline in consumer demand caused by the cost of living crisis, oversaturation of the market, and an increase in the diversity of their product market.
On parity with other major industries, the sector has subsequently developed a heightened interest in how it can minimise its environmental impact and implement more sustainable practices throughout the entire value chain.
Great expectations trigger positive changes
When it comes to optimisation and sustainability, it’s not just the beer production and processing that needs to be taken into account. Growing and malting grains, refrigeration, storage, and shipping of the product all create greenhouse gas emissions.
This is precisely why Australian breweries are increasingly taking affirmative action to make their operations more sustainable, by pledging to reduce their existing annual carbon footprint by anywhere from 15,000 to 120,000 tonnes. That’s the equivalent of 2,960 to 23,683 homes’ electricity use for an entire year.
In 2020 Lion’s Australian operations became the country’s first certified large-scale carbon-neutral brewer. Asahi became the first Australian major beer manufacturer to commit to 100% renewable electricity in December 2023, with a commitment to source 100% of purchased electricity from renewable sources by 2025.
Together, they started the wave of beer manufacturers in Australia changing course to lower their energy bills and reduce their carbon emissions.
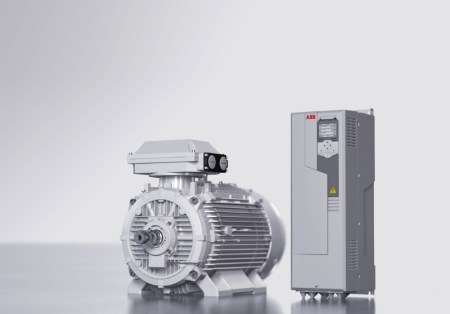
Where the opportunities can be found
Variable speed drives (VSDs)/variable frequency drives (VFDs), motors, and PLCs are indispensable for key processes in beer manufacturing, and play a critical role in generating energy savings, improving productivity, and reducing costs. ABB’s advanced solutions of energy-efficient motors, drives, and PLCs, enable breweries to increase yields, reduce downtime and minimise waste. They can also enhance sustainability and safety across the entire operations value chain, from raw ingredient production and brewing to storage and logistics.
The right technology can positively affect the growth phase of fermentation, as temperatures can be more carefully controlled to ensure precision for a more consistent product. Meanwhile, high-efficiency motors can significantly reduce the energy usage and costs of running fans and blowers.
At the brewing stage, high-intensity applications like mixers and decanters can be operated more smoothly using drives, reducing downtime and maintenance requirements whilst their integrated safety features help to keep personnel out of harm’s way.
And the return on investment (ROI) implications are significant. Adding variable speed drivesand high efficiency motors to different applications in this way can help manufacturers reduce energy use by as much as 50%, bringing costs down steeply.
Additionally, drives can play an important role in enabling data-led decision-making by providing key data in real-time. By coupling a drive with a sensor, essential information is monitored, meaning data on the condition and performance of equipment can be collected. With this data-driven insight, companies can pinpoint ways to reduce waste, keep operations running, and enhance energy efficiency.
For logistics and storage, high precision PLCs and drives can ensure that products are moved smoothly from place to place, reducing the likelihood of breakages and waste, while providing seamless synchronization.
Don’t cut corners when it comes to safety
When it comes to ingredient and personnel safety in beer production, it’s essential to make plant and personnel safety a top priority. These harsh environments go hand-in-hand with tackling diverse safety demands. Employees should never be exposed to hazards: from operating centrifugal blowers and cleaning and maintaining mixers, to risks associated with hot liquids and process steam.
Using best-in-class technology like remote monitoring protects personnel from potentiallydangerous processes. Those with advanced functions, like safe torque off, make suredecanters, conveyors, and mixers come to a fast and effective stop when needed, particularly in emergencies. For example, safe torque off (SIL3) prevents unexpected movement of conveyors.
The best dust ignition-certified engine and variable speed drive/variable frequency drive packages comply with the demands of dusty and explosive environments, for example in areas where malt is stored.
Food and beverage safety and hygiene requirements demand harsh washdown protection. Food Safe motors allow food and beverage manufacturers to meet hygiene requirements without compromising on reliability and productivity.
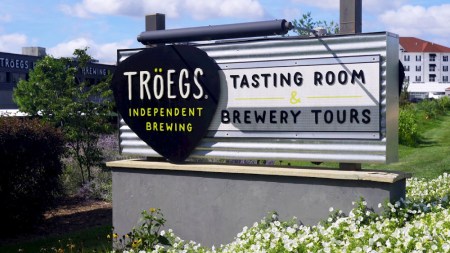
News waves of sustainability for the future
ABB Australia Division Manager for Drives Products and System Drives Rajesh Maker says, “ABB has a proven track record of delivering effective solutions right across the brewery value chain. Our technology has been engineered for reliable operation in demanding environments, and our local team of experts are always ready to help brewers optimise production yields and more importantly, reduce their environmental impact.”
As the industry moves towards achieving greater sustainability, it is adopting innovative methods like converting waste into biogas, using recycled packaging materials, and reusing water. By implementing already available technology, companies can accelerate the creation of a Net Zero operational model, whilst ensuring personnel safety and productivity remain at the forefront.
Download our Breweries Solutions Guide and discover how ABB can help optimise your operations.
Ready to get started? Check out these projects in the F&B industry delivered by ABB Australia and contact us today.